摘要:当前,光伏电站普遍存在熔丝故障多、维护工作量大等问题。本文就光伏熔丝的失效机理、应用场景、保护原理与实践等通过理论分析与现场考察相结合,分析了直流熔丝应用于光伏电站的失效率、安全可靠性风险等,供广大从业者参考借鉴。
关键词:光伏,熔断器,热疲劳,反灌电流,直流拉弧,运维
1.前言
笔者作为光伏从业人员,在走访电站期间,经常会看到运维人员奔波在子阵间去更换熔丝,也经常会看到烧毁的熔丝盒及接线端子。那么光伏中为什么要使用熔丝?在使用中存在哪些问题?有没有更好的解决方法?带着这些疑问,笔者经过大量的信息搜集,现场调研,掌握了光伏熔丝的一手资料,供业界同行参考。
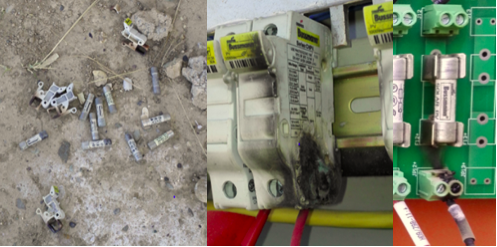
图1 失效的熔丝、烧毁的熔丝盒及接线端子
2.熔丝概述
熔丝,也称为保险丝、熔断器,它是一种串联在电路中,保障电路安全运行的元件,广泛用于配电系统和控制系统,主要进行过电流保护。熔丝的结构如下图所示,其工作原理都是利用金属的热熔特性。
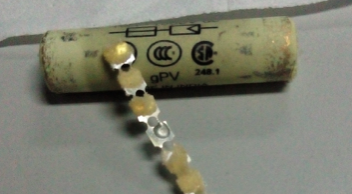
图2 光伏熔丝内部结构
2.1熔丝的发展历史
熔丝的使用历史超过了100多年,最早的记载出现在1864年,当时熔丝被用来保护海底电缆。光伏熔丝是随着光伏产业的发展而出现,其国标GB/T13539.6在2013年发布,是一个相对比较新鲜的事物。其标准及产品设计还处于不断优化的过程中,并不成熟,实际应用中质量难免出现问题。
光伏熔丝的设计难点在于体积小(1038mm),直流高压灭弧难。前两年,国内很多企业都认为在这么小的体积上做到1000Vdc是不可能完成的事情,这也从侧面反映了光伏熔丝的设计和制造难度。
2.2熔丝在光伏中的应用
光伏中为什么要使用熔丝,熔丝在光伏中起到什么作用?
在光伏电站用,不采用断路器,采用熔丝,最主要的原因是降成本。直流断路器贵,价格是熔丝的5倍。因此集中式电站、部分组串式解决方案和目前刚推出的集散式方案,都不约而同的采用了大量熔丝。
以典型的集中式电站为例,在当前的集中式电站中,并联的组串数量高达100串,当有一串发生短路故障,所有组串的电流均会反灌故障组串,反灌电流可能超过800A,远远超出了线缆和组件的安全要求,易引发火灾事故,所以必须使用熔丝来切断故障电流,保护线缆和组件。
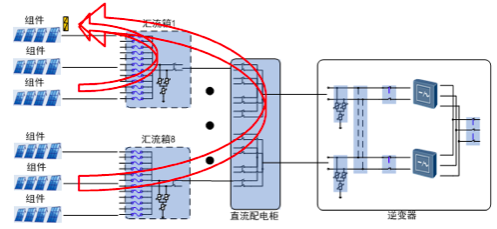
图3 集中式光伏组件故障时的电流流向
相比集中式、集散式方案,当前部分厂家的组串式电站方案是没有使用熔丝的,他们是如何进行保护的呢?
该组串式方案最多2串组件并联,即使有一串发生短路故障,反灌电流最大也不会超过10A,所以是安全的,无需熔丝进行保护。
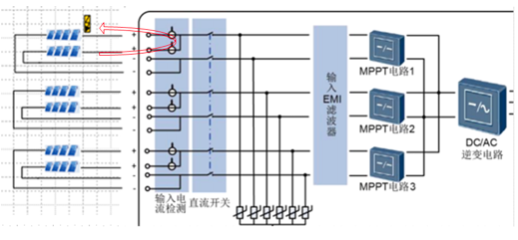
图4 组串式光伏组件故障时的电流流向
3.熔丝在光伏应用中存在的问题
笔者走访了大量电站,发现熔丝在每个电站都存在一些问题,本文主要从熔丝的安全风险和熔丝失效造成的损失等方面进行分析。
3.1熔丝增加了直流节点,埋下安全隐患
集中式1MW需要使用熔丝400个,每个熔丝与熔丝盒夹片之间有2个接触点,每个熔丝盒与接线有2个接触点。所以每个熔丝将有4个接触点,集中式因使用了熔丝就有1600个直流节点。熔丝盒对线缆可靠安装要求高,现场实际不容易做到,经常出现接触不良的现象,引起烧毁或者直流拉弧,是汇流箱着火的主要原因。
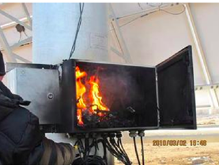
图5 直流汇流箱着火
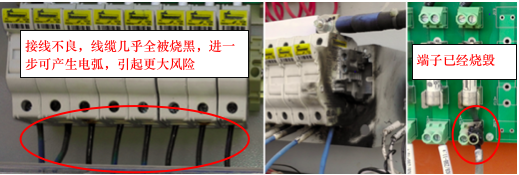
图6 熔丝接线不良引发的烧毁着火案例

图7 熔丝与底座接触不良
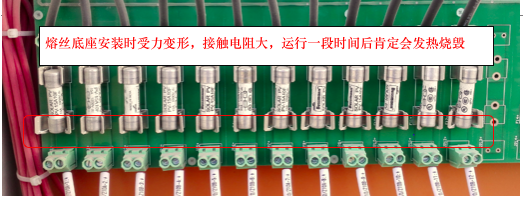
图8 熔丝安装质量堪忧,一段时间后肯定会发热烧毁
3.2熔丝在低倍过载时,熔断慢,发热高,存在着火风险
熔丝的保护原理是利用金属的热熔特性,这一特性决定了熔丝的熔断时间与过电流的大小呈反时限的关系,电流越大,其熔断时间越短,电流越小,其熔断时间越长。电池板的电流受天气影响,大小不可控制,当熔丝处在小电流过载时,其熔断时间将变得很长,在这种“将断未断”的情况下,熔丝将处于一个非常高温的热平衡状态。这么高的温度将破坏线缆和熔丝盒的绝缘,最终引发着火事故。
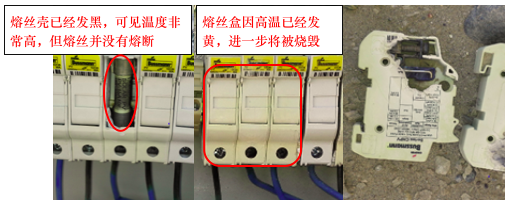
图9 熔丝发热使熔丝盒烧毁
另外,部分熔丝在熔断时会出现喷弧现象,电弧温度非常高,会使相邻的塑料元件、线缆绝缘等着火。
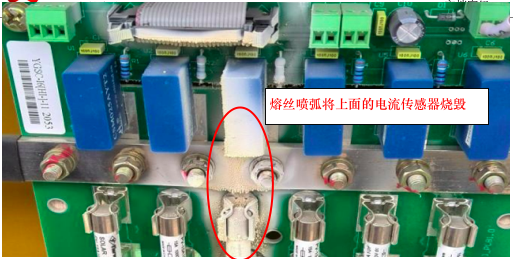
图10 熔丝熔断时喷弧烧毁相邻元件
3.3熔丝并不能有效地保护组件
熔丝的工作原理是利用金属的热熔特性,那么15A的熔丝肯定要在大于15A的电流下才能够熔断,那么到底是多大的电流呢?笔者查阅相关标准,得到了如下答案:15A的熔丝,标准要求在16.95A下(1.13倍),1小时不能熔断,在21.75A下(1.45倍),1小时内熔断。
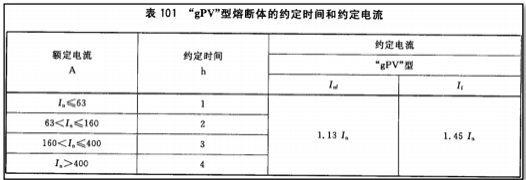
图11 标准IEC 60269-6 对熔丝的要求
组件有一个参数是“最大保险丝额定电流 15A”,那么组件的这个参数是怎么来的,代表什么意思?笔者查阅相关标准,得到了如下答案:最大保险丝额定电流15A的组件,标准要求在20.25A(1.35倍)下,2小时不能燃烧。值得一提的是,标准只是要求组件不起火,却不能保证组件不损坏,实际上组件一直在承受反向电流而发生热斑效应,性能会下降,输出功率会降低。
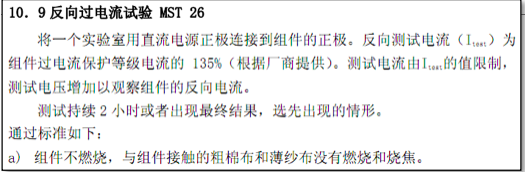
图12 标准IEC 61730-2 对组件的要求
从上面可以看到,熔丝的标准要求是1.45倍的电流熔断,而组件的标准要求是1.35倍的电流,那么在1.35倍到1.45倍之间就出现了一个保护空挡。在这个保护空挡内,熔丝不能够有效地保护组件,可能出现组件着火的严重事故。
从前文光伏熔丝熔体结构上可以看出,熔丝狭径非常细,对制造工艺要求很高,普通厂家很难控制好熔丝的质量。若生产的熔丝偏大,不能够在规定的电流和时间下及时熔断,更会加剧组件的损坏,带来着火风险。
笔者听闻2014年青海及内蒙电站先后出现过多块组件损坏的问题,有可能就是熔丝没能及时的熔断,使组件承受了长时间的反向电流导致。
3.4熔丝在电站的失效率统计
笔者利用走访电站的机会,与业主多次交流熔丝失效的问题收集了一些熔丝失效数据,经过汇总整理如下:
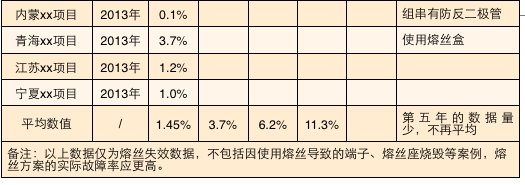
根据熔丝失效率统计的数据,经过拟合分析,熔丝的失效率符合随工作年数逐年上升的趋势,5年以后失效率超过15%。
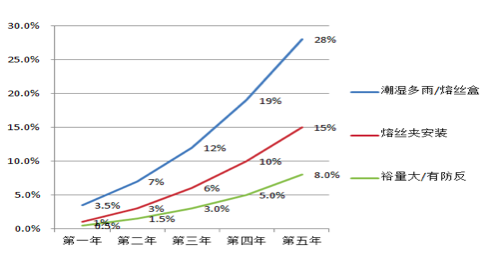
图13 熔丝失效率拟合曲线
光伏熔丝为什么会频繁失效,笔者认为熔丝老化致使通流能力下降是主要原因。在光伏应用中,昼夜温差大,每天一次的高低温循环会显著加速熔丝的热疲劳效应,降低熔丝的通流能力,缩短熔丝寿命。
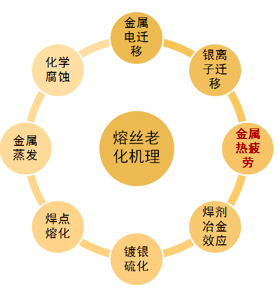
图14 熔丝老化机理
3.5熔丝失效造成的发电量损失
熔丝一旦失效,那么这一串的发电量肯定就要损失了,更换的时间快,发电量损失的就少一些,更换的时间慢,发电量损失的就多一些。目前,国内大型地面电站更换熔丝的平均时间在15天左右(通讯断链或没有使用智能汇流箱,一个月才能检查一轮),山地电站时间更长,有个别项目甚至半年才会检查一次,发电量损失严重。当然也有几天完成的,前提是监控稳定,能够从后台清晰看到熔丝的状态。
按照1MW子阵为单位,第五年开始因熔丝失效造成的发电量损失1.5%以上,假设电价为1元/kWh,每年将造成收益损失至少22500元。以熔丝市场价格12元每支进行计算,物料更换成本至少720元。
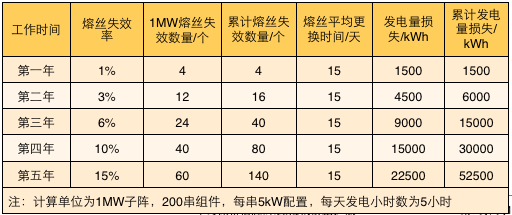
上面表格中的数据并没有包含人工运维成本,若电站没有使用熔丝,无需更换熔丝这一项工作,每50MW能够减少一个运维人员的话,那么可节省开支7万多元,分摊到每MW也有1500元左右。人工运维成本,加上发电量损失,熔丝物料成本,每MW因熔丝失效每年将损失至少25000多元。100MW电站25年的损失将至少5500万,这还不包括因熔丝造成的着火事故损失,实际损失将更大。
4.总结
经过以上分析,笔者得出以下几条结论:
1.熔丝方案增加了直流节点,经常出现熔丝盒、接线端子、线缆等烧毁的事故。
2.熔丝在低倍过载电流情况下,熔断慢,发热高,存在着火风险。
3.由于熔丝和组件之间存在保护空挡,熔丝并不能有效地保护组件。
4.熔丝失效率逐年升高,5年以后失效率超过15%,发电量损失1.5%以上。
5.100MW电站25年因熔丝失效造成的损失将至少5500万。
在雾霾成为人们“心肺之患”的今天,变革传统能源结构,发展太阳能等清洁能源成了人们最急迫的呼声,光伏电站建设也迎来了前所未有的投资机遇。安全是光伏电站的命脉,也是取得投资回报的根基所在,特别是在山地、屋顶等与光伏结合的项目上,安全几乎是一票否决的原则问题。
不管是集中式方案,还是集散式方案或部分组串式方案,因电站中使用大量的熔丝,埋下了安全隐患,易引发着火事故,成为光伏电站安全的“头号杀手”。使用熔丝可以降低成本,但熔丝的高失效率,不仅造成了高额的发电量损失,也为电站运维增加了难度,反而得不偿失。只有采用类似上文中提到的最多2串组件并联的组串式方案,才是安全的,无需熔丝进行保护。这种无熔丝的组串设计方案,不仅从源头解决了组件和线缆的保护问题,而且彻底根除了因使用熔丝带来的安全风险和失效损失,相信会是电站更好的选择。
参考文献:
[1] 石颉, 李烨刚, 施海宁等. 熔断器熔断体老化失效的物理分析. 低压电器, 2010.
[2] 王季梅. 低压熔断器. 北京:机械工业出版社, 1979.
[3] 国家能源局. 关于光伏产业监测有关情况的会议通报, 2015.
[4] 吴庆云, 梁利娟. 太阳能光伏系统保护用熔断体标准分析. 低压电器, 2013.
[5] 刘滨. 光伏电站建设及运营管理分析. Silicon Valley, 2014.
特别声明:索比光伏网转载其他网站内容,出于传递更多信息而非盈利之目的,同时并不代表赞成其观点或证实其描述,内容仅供参考。版权归原作者所有,若有侵权,请联系我们删除。凡来源注明索比光伏网或索比咨询的内容为索比光伏网原创,转载需获授权。